Enabling works, site clearance and fast-track construction of a 58,000 m² Regional Distribution Centre in Newbridge.
Project Overview
The Lidl Regional Distribution Centre in Newbridge is Lidl’s largest single investment in Ireland since entering the market. Employing more than 350 people, it will act as a major base for Lidl’s distribution arm to their stores nationwide. The warehouse building and associated two-storey office wing was delivered to an extremely aggressive 12-month programme and has a gross floor area of 58,000m², is 3 times the size of the Aviva stadium, and is nearly half a kilometre in length. It is one of the most sustainable and energy efficient logistics centres in Europe, with an A1 energy rating and meeting BREEAM Excellent standards in design and construction.
The enabling works package involved contractor designed ground improvements, along with all drainage ducting, and security fencing over a 130,000m² site area. All works were fast-tracked to achieve the client’s programme, allowing the follow-on contractor to commence with the building works.
We undertook the design of the earthworks solution by proposing a ground improvement solution involving a lime and cement stabilisation technique. This involved the excavation of approximately 320,000m³ and mixing the as-dug material with lime and replacing the material to exceed 100Mpa. This eliminated the need to dispose unsuitable material from site. Our project team worked with a lime, cement ground improvement specialist to achieve a design that enabled the building to be supported directly on the stabilised fill material, thus eliminating the need for piles. We also improved and stabilised the surrounding yards area, reducing the volume of excavated and imported fills.
The bulk earthworks were completed within five months, with an average of 3,000 to 4,000m³ of material excavated, stabilised, and backfilled daily. The maximum output achieved was 5,100m³/day. Borrow pits were also excavated on-site allowing suitable material (Class 2) to be utilised for the project and poorer quality class UA material to be buried on site. This offered a cost saving to the project and eliminated any UA material from being disposed of off-site. The location of the borrow pit was determined by undertaking a mass of additional ground investigations to determine the most suitable material on-site.
All main drainage works were completed immediately after the ground improvement was undertaken. It was important that any excavation through the lime / cement stabilised fill was excavated as soon as possible prior to the material gaining full strength. This required extensive coordination on-site. We also undertook a complete review of the client’s proposed drainage solution and proposed, and then designed, an alternative drainage design utilising Tubo-sider pipework. This allowed a high percentage of the drainage water to be stored within the main drainage system, eliminating the needs for alternative attenuation systems on an already restricted confined site. Over 4,200lm of 1.4m in diameter Tubo-sider pipework was laid as an alternative to the standard drainage proposed by the client.
All works were completed under a fast track programme, with the main building structure commencing just 12 weeks after the initial site clearance commenced. An agreed phased handover programme was agreed, resulting in the project being split up into four cells. Each cell consisting of a footprint of 13,800m² with an earthworks excavation and backfill volume of approx. 48,500m³ per cell.
Key Features
- Enabling works for the construction of a 58,000m² high-bay regional distribution centre
- Contractor designed ground improvements, drainage ducting, and security fencing over a 130,000m² site area
- Site clearance including demolition of several buildings
- Contractor designed lime and cement ground improvement technique involving a bulk excavation of over 320,000m³
- Structural fill designed to be sufficient for pad and loading for the super flat floor (55,000m²)
- Construction of 515 building foundation pads involving over 3,750m³ of concrete
- 4,000lm of 1.2Ø drainage including a design and build tubosider attenuation pipework
- 8,000m of ducting / 60,000m² of external concrete paving / 20,000m² of asphalt paving
- Extensive silt mitigation measures, including several temporary settlement lagoons
- Full dewatering geotechnical design implemented
- 2,000m of Trief containment kerbing
- BREEAM "Excellent” rating
- 2020 Irish Construction Industry Awards - Overall Construction Project of the Year and Industrial Project of the Year
- 2022 CECA Excellence Awards - Best Health and Safety Initiative
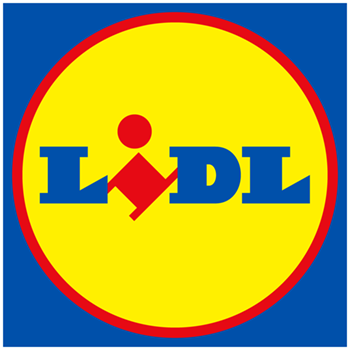
Project Team
Client:Lidl Ireland GmbH
Architect:
SDS Engineering / MCA Architecture
Quantity Surveyor:
CQS Group
Structural Engineer:
SDS Engineering
M&E Consultant:
J.V. Tierney & Co
Project Details
Contract Value:€20 Million
Floor Area:
130,000m²
Duration:
10 months